Guys,
This is adding the photos and process for making the blank tumbler as was posted on the topic "tumbler mill", just to keep this topic complete. Eventually this will be changed over to a tutorial.
To make the tumbler I forge a blank from W1 tool steel, the same stuff as 1095 steel. The forging looks a lot like a large nail with an off center head. To help in the forging I use an iron bar with a through hole as a big stake setup to forge the head.
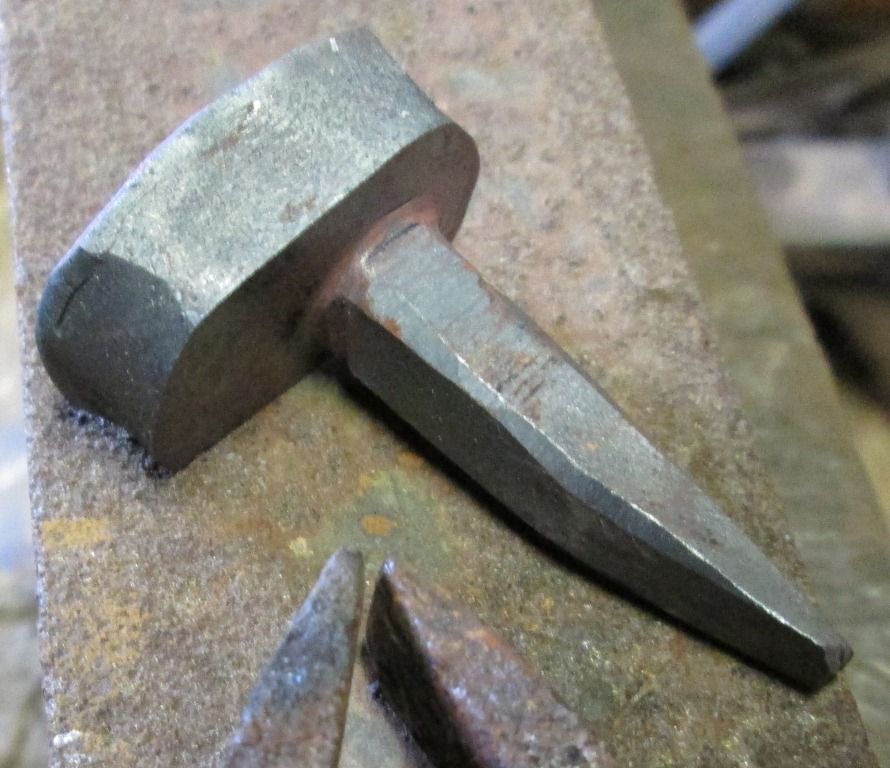
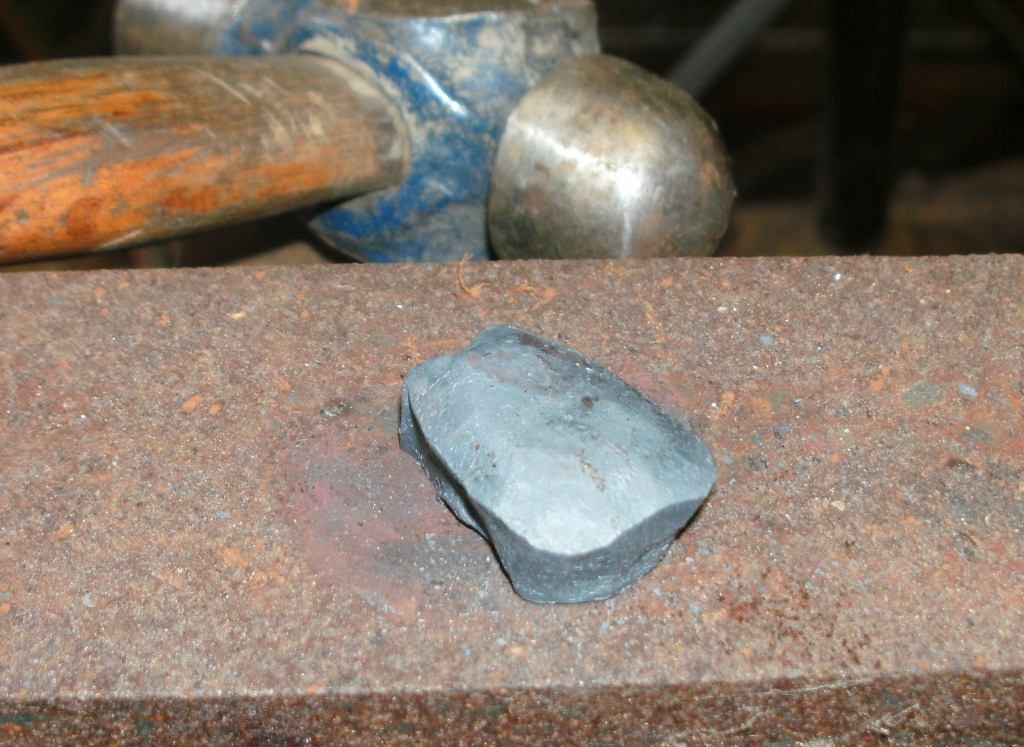
The tumbler mill is made using two opposing cutters that are screw adjustable. The stops on the screw threads are set to give the proper tumbler thickness.
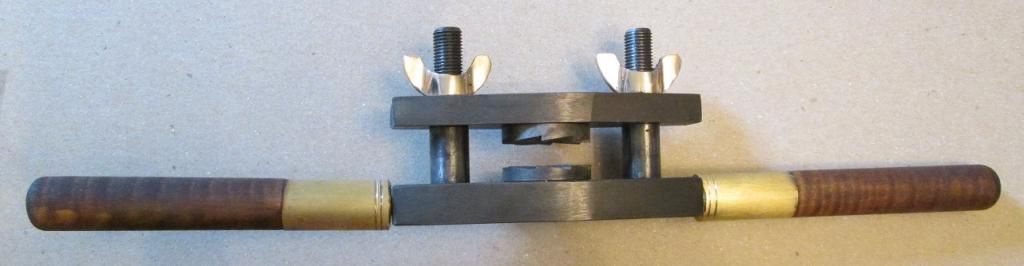
The tumbler blank axle is filed to a slightly tapered round section that will pass about halfway through the mill large axle cutter. The blank is clamped in a vise with the axle pointing up. The lower half of the mill is then used to cut the axle to the proper diameter until the cutter contacts the head. The cutting action is a lot like using a typical die stock.
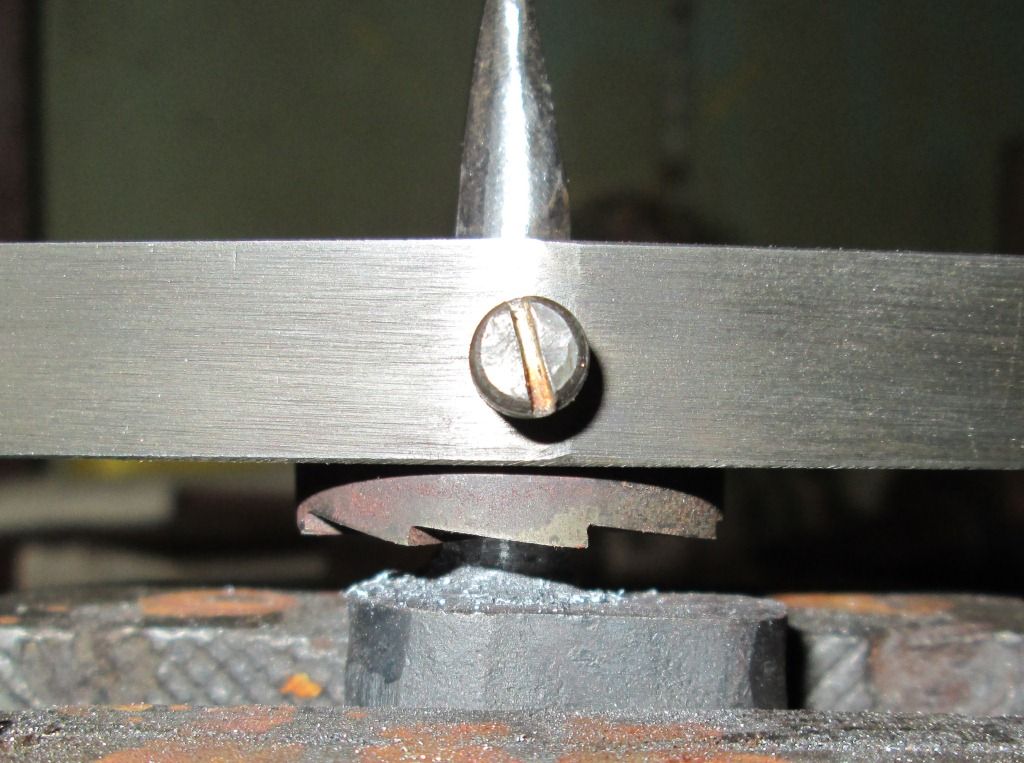
Now the entire mill is assembled and the tumbler blank axle is clamped in a vise. The screws are used to tighten the cutters against the forging and the whole tool is turned to begin cutting.
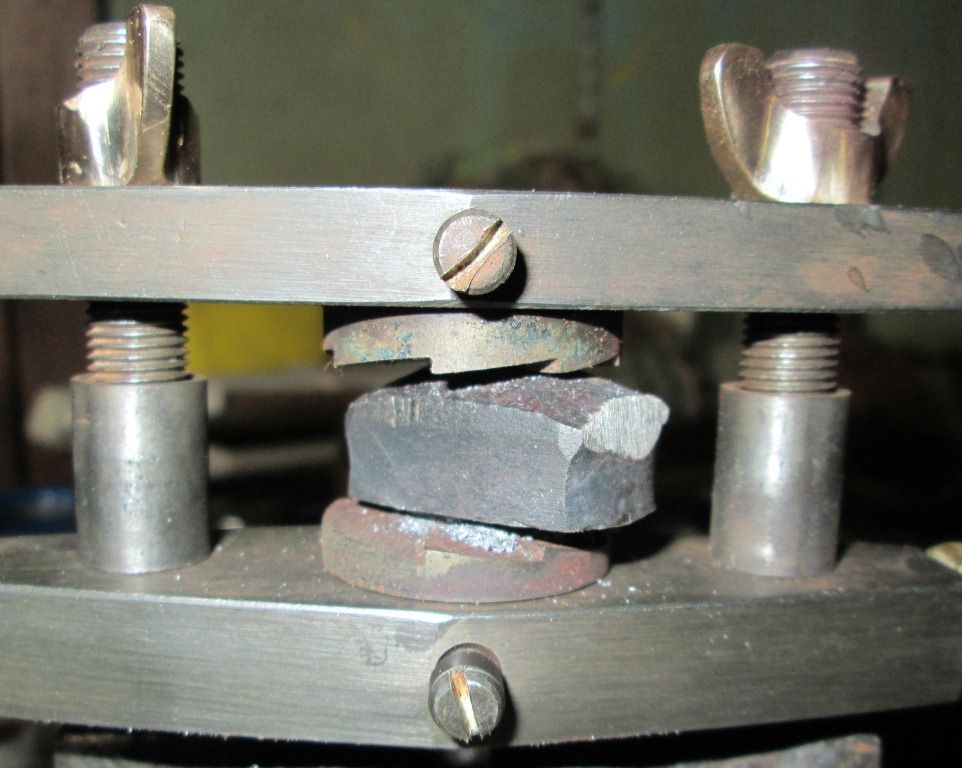
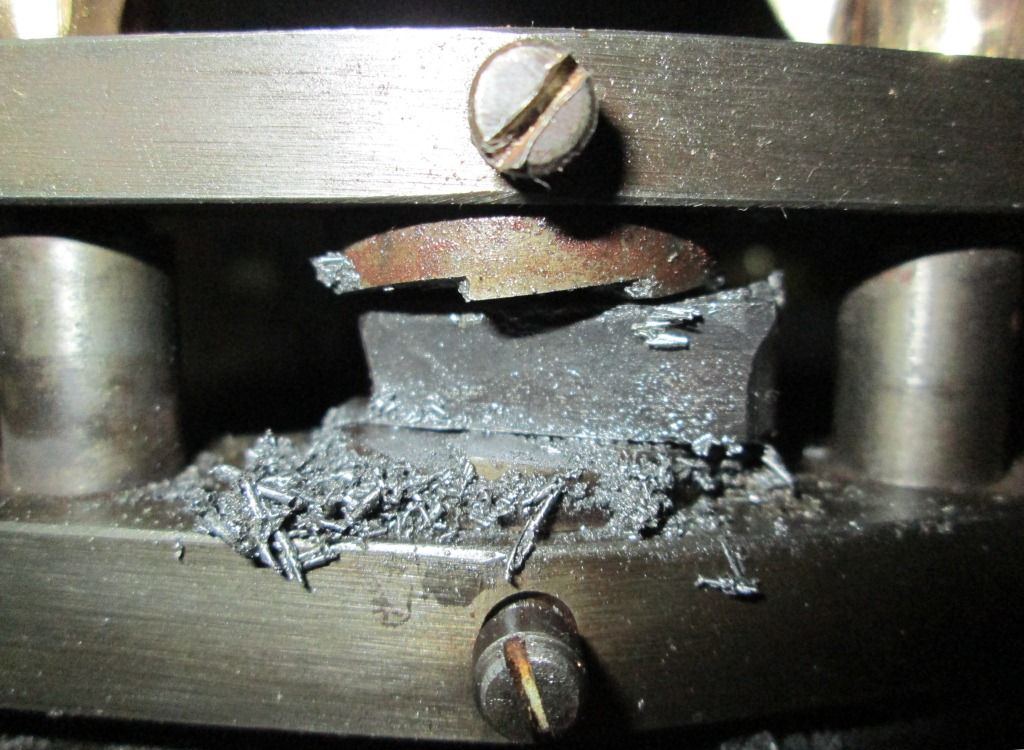
Much of the use of the tumbler mill is to mark the forging for a guide to use a coarse file to remove most of the metal. Here is a photo of the partially finished forging where you can see the circular cut marks from the mill and the file marks from the rough shaping.
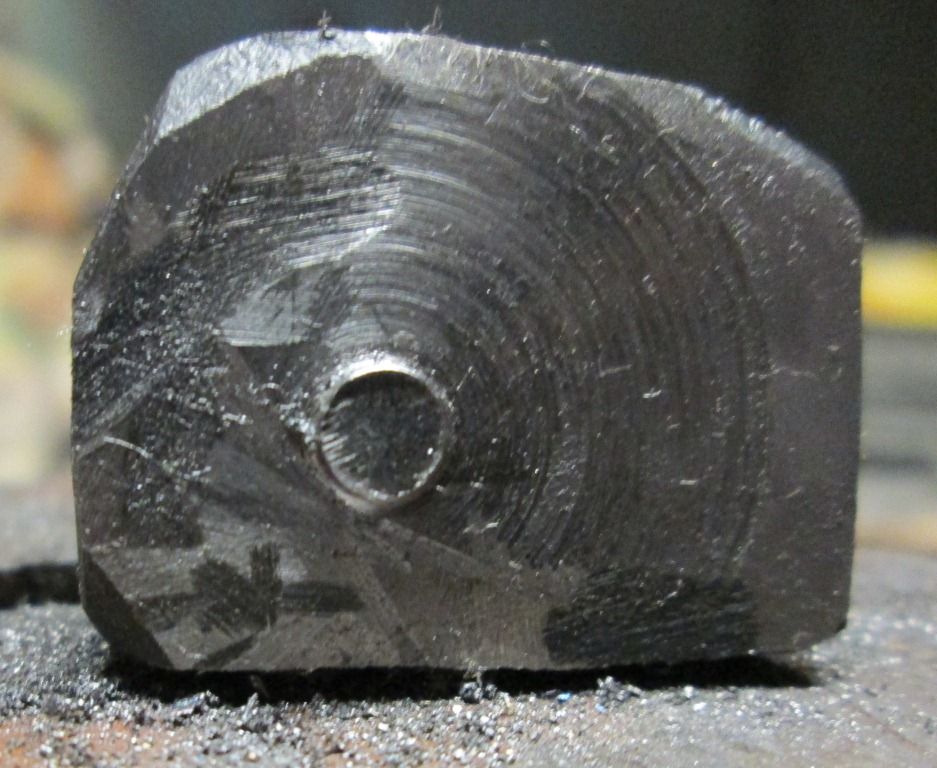
Now is the time to cut the rough shape of the outside edge of the tumbler. Now the final cut is made and the process of using the tumbler mill is finished when the screws bottom out on the stops.
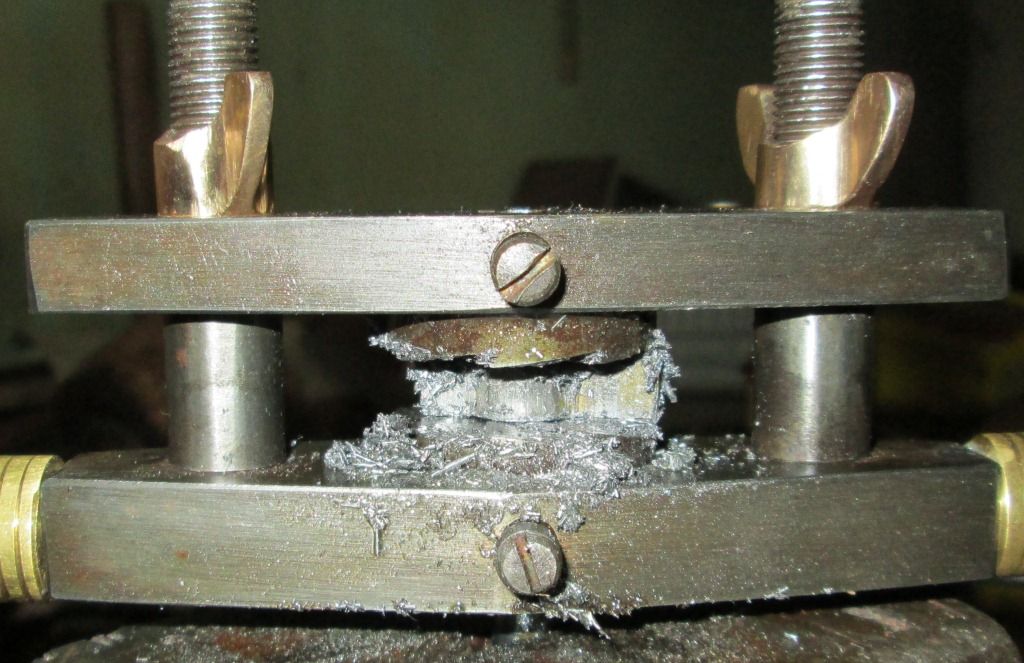
Here is the finished tumbler blank.
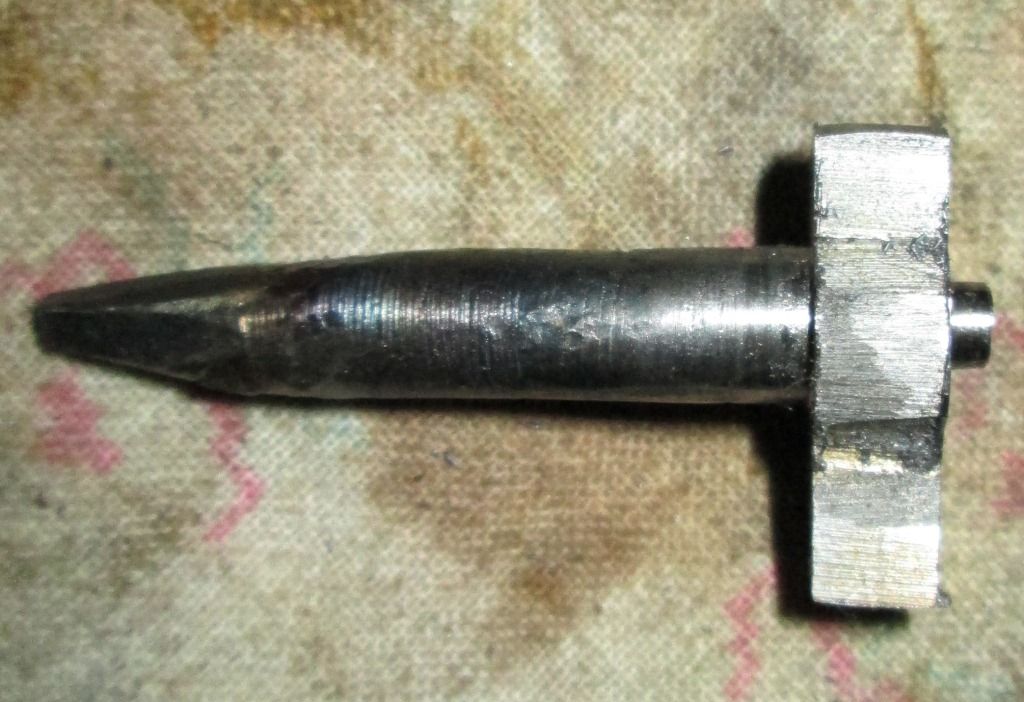
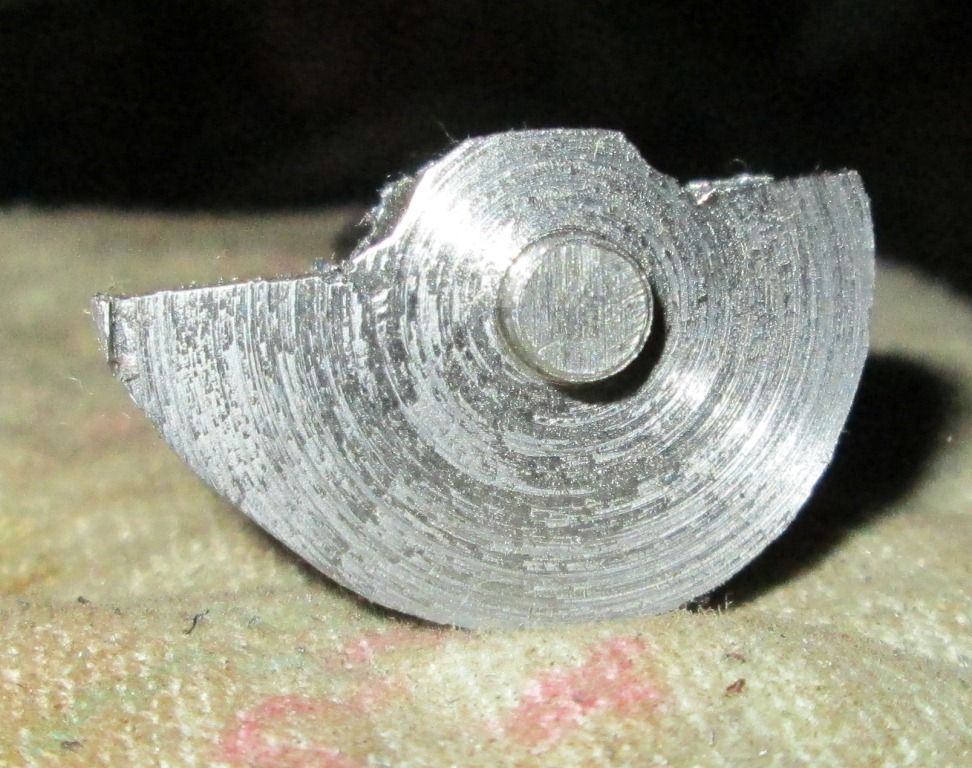
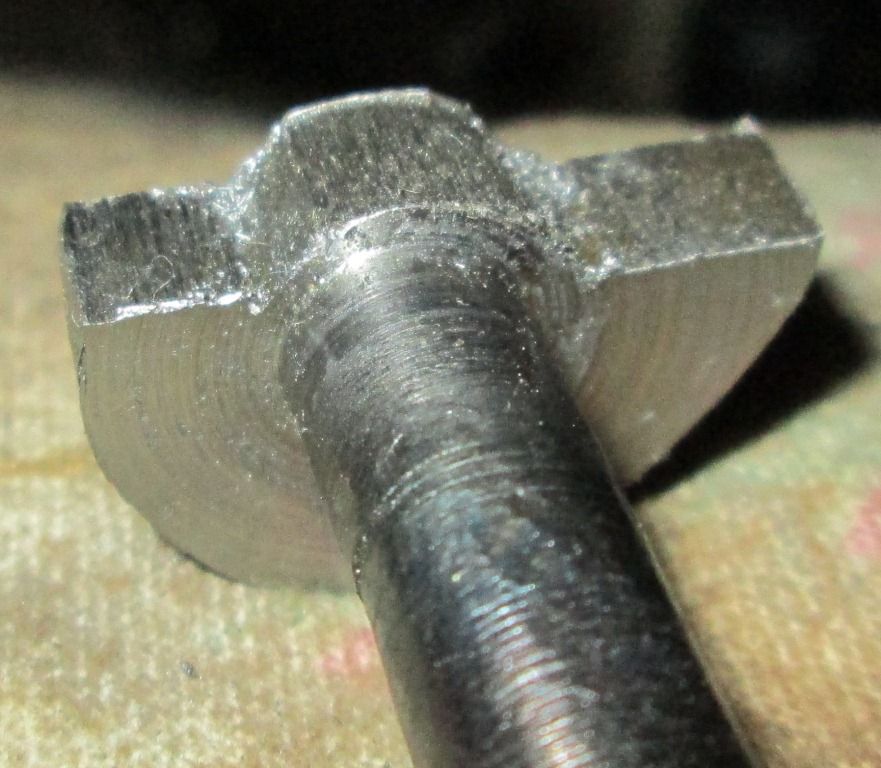
Jim