More on the rib. Here is the thimble cut into the rib. The tight fitting dowel has an aluminum heat shield and exactly aligns both thimbles to the rib contour for soldering. The thimbles and rib cuts are tinned, the thimbles clamped in place with C-clamps on the dowel, and then soldered.
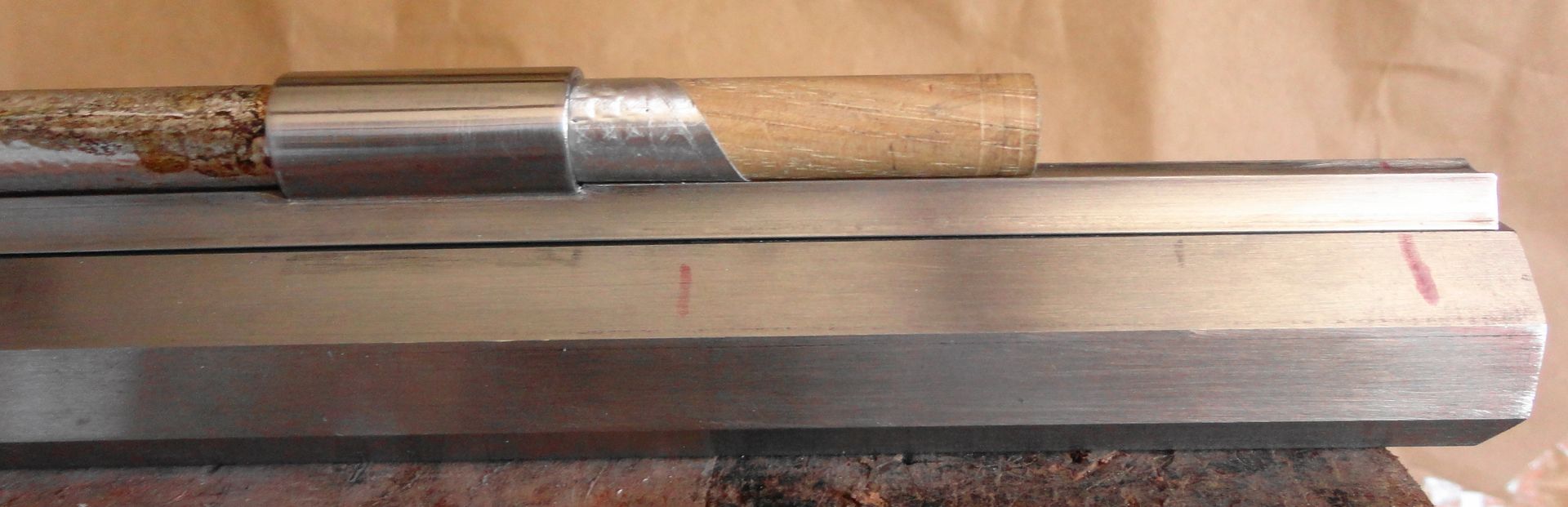
The soldered thimble, .530 inside diameter, cleaned up. Takes a hand made hickory rod.
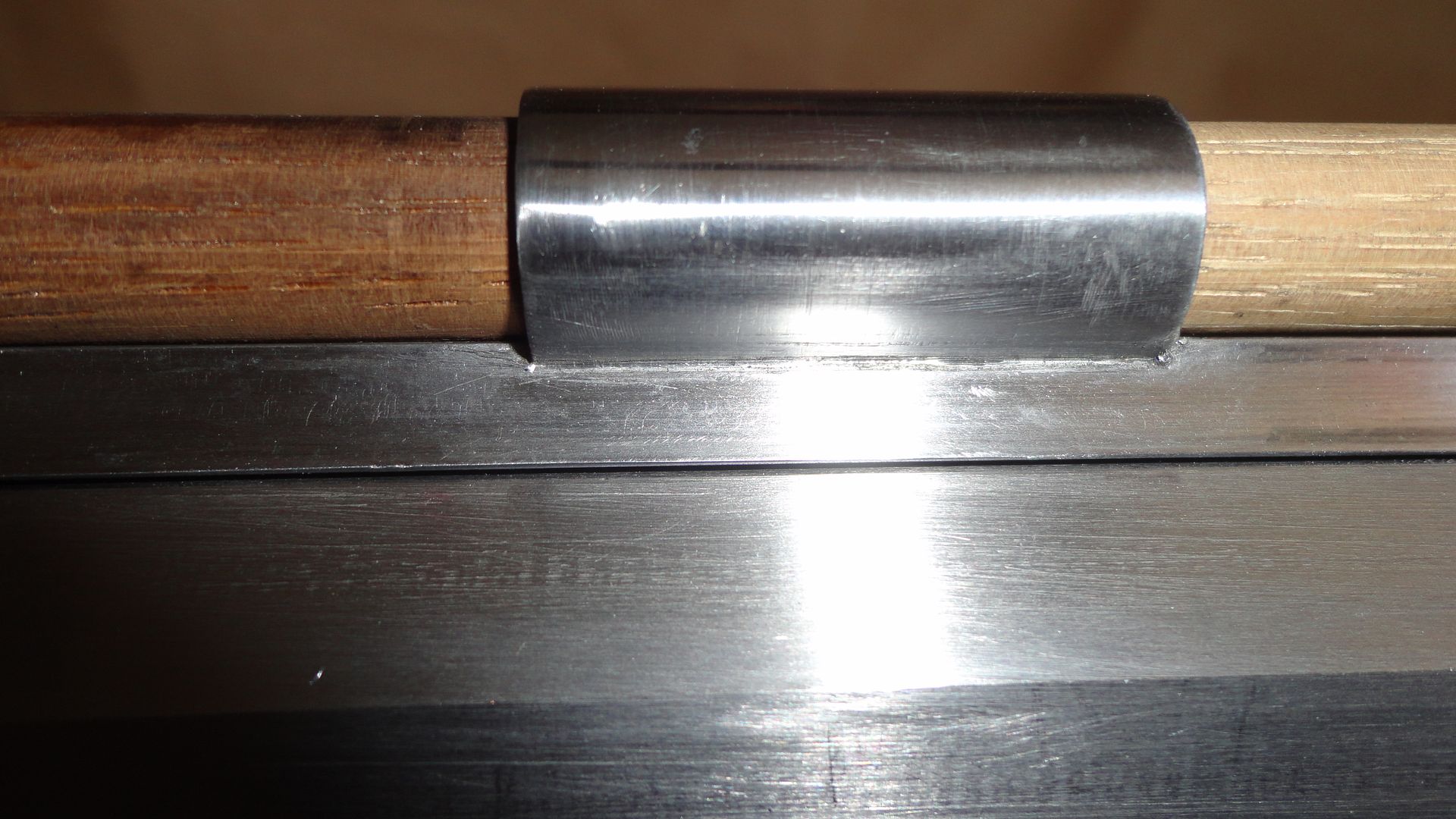
The end of the solid rib is ground back and the half-moon is filled with solder. The metal backing is non-magnetic, solder doesn't stick to it. The original Hawken ribs were hollow, some lipped, and the solder plugged the end. I simulate this. The Robidoux Hawken (see it on Antique board) has the front screw missing, there is a 1/8" hole. Yet the rib is solid. So the solder must solder the rib to the end of the barrel.
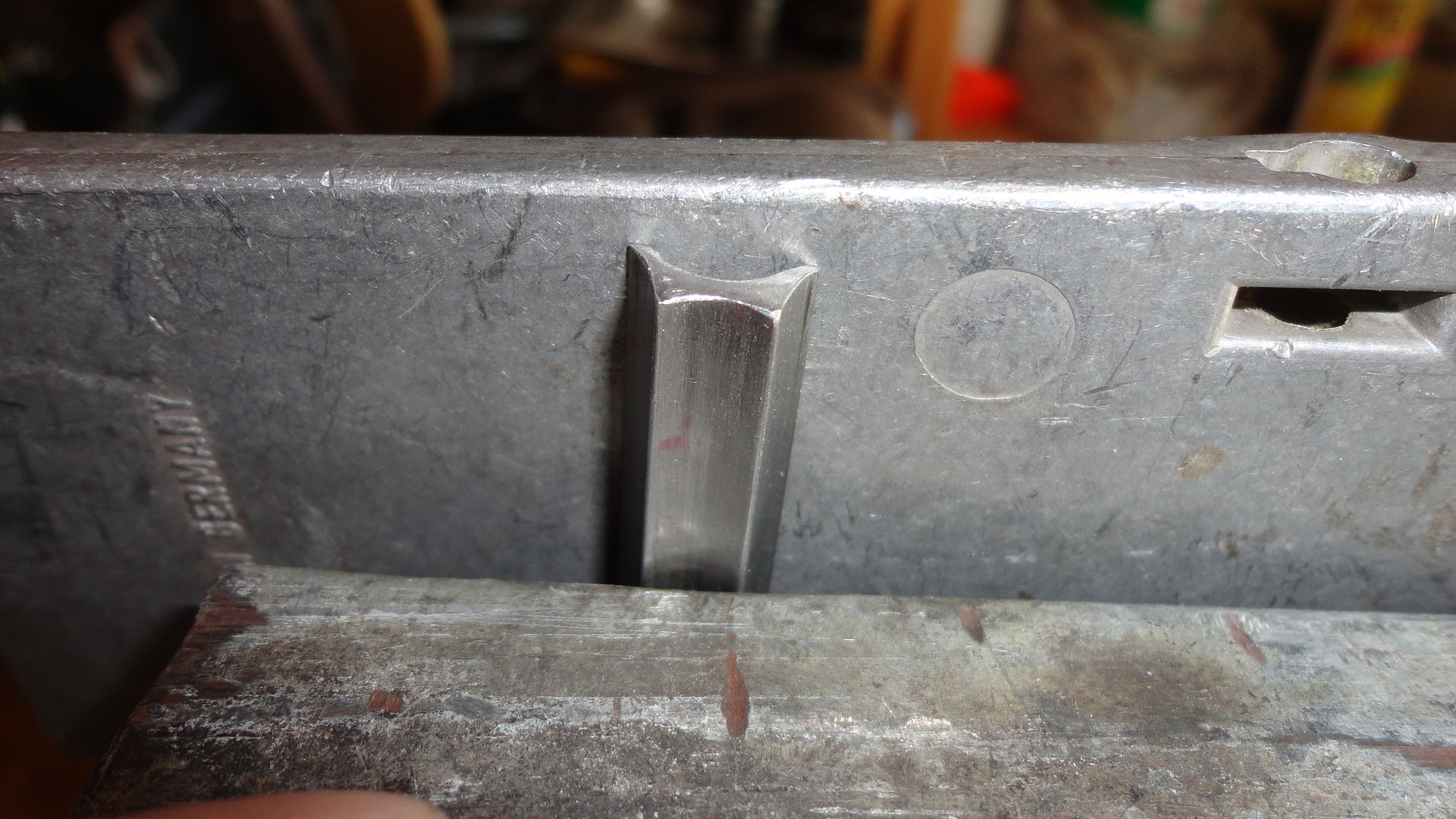
There were 4 rivets in the original Bridger. First I drilled the holes in the rib for the rivets, which I pounded out of 1/4" thick copper to round, about .220 diameter, not having any large copper wire. The rib was then put in place and clamped down. The drill was indexed exactly to the hole . With the table level, I adjusted the quill until the drill just touched the barrel in the full down position. You can leave the chuck loose, pull the quill down to touch the barrel, which pushes the drill up in the chuck. Then tighten the chuck. Then I put the two shims, .150" thickness, under the barrel, aligned the drill with the rib hole and drilled the hole. Did all four. Then I removed the rib and drilled the holes there to the next larger size for clearance of the rivets.
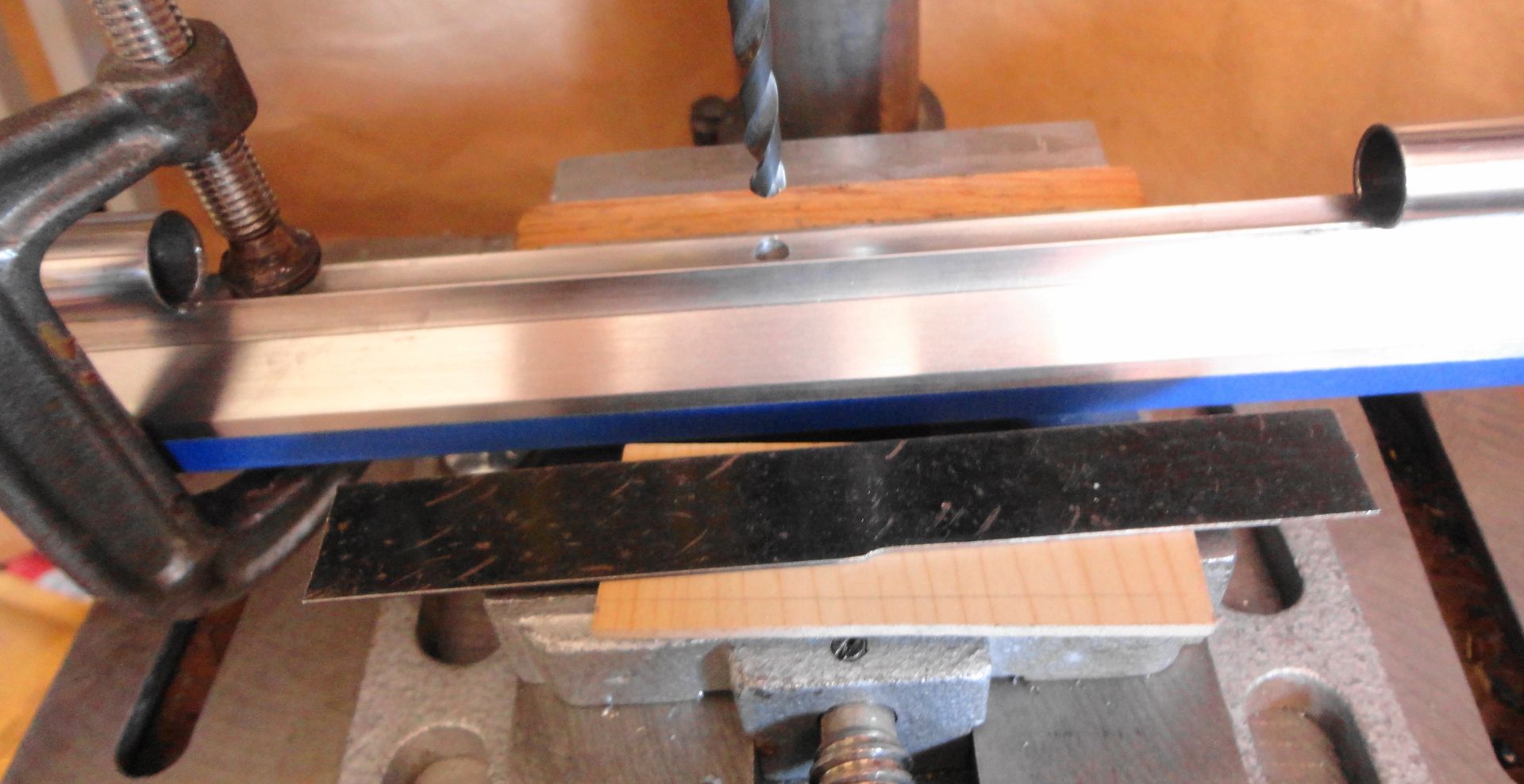
This should be a vertical photo, but you can look at it sideways! These are copper rivets I made. A small groove is cut to be just below flush, the holes have Permatex Sleeve Retainer (glue) put in, then the rivets are peened home. The barrel is an .54 caliber 1 1/8" 7-groove by Oregon Barrel Company, exactly made for a 1/2" long 3/4x16 breech plug. A very nice barrel. I had them make it 34" long but then I cut it with hacksaw and files to 33 1/4" like the original, which has no crown or rounded edges. I expect to file the muzzle like the original. The lands and grooves both get filed back about 3/4". I have not done this before and am leaving this for last.
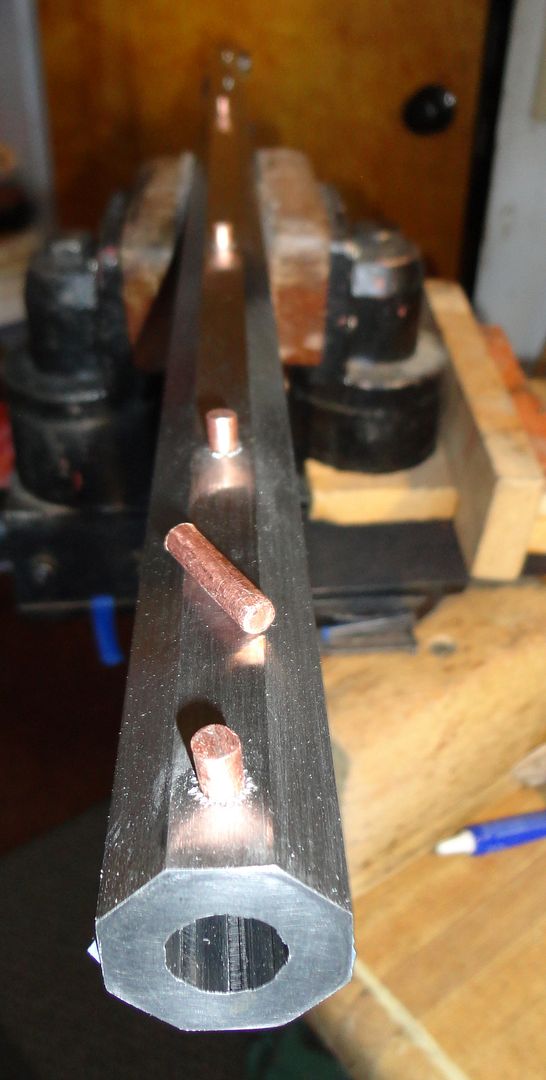
I did not try the rib for exact fit, afraid I might not be able to get the rib off again. I put Permatex on the barrel flat and the bottom of the rib, fitted the rib over the rivets and clamped it solid. Waited 24 hours for curing.

Here the Permatex is cured and the rivets peened over. They get filed flush. I have since learned that Lowes has bulk copper wire 3/16" in diameter and one size larger. A friend gave me a foot of the 3/16", I'll use that or the larger size next time.
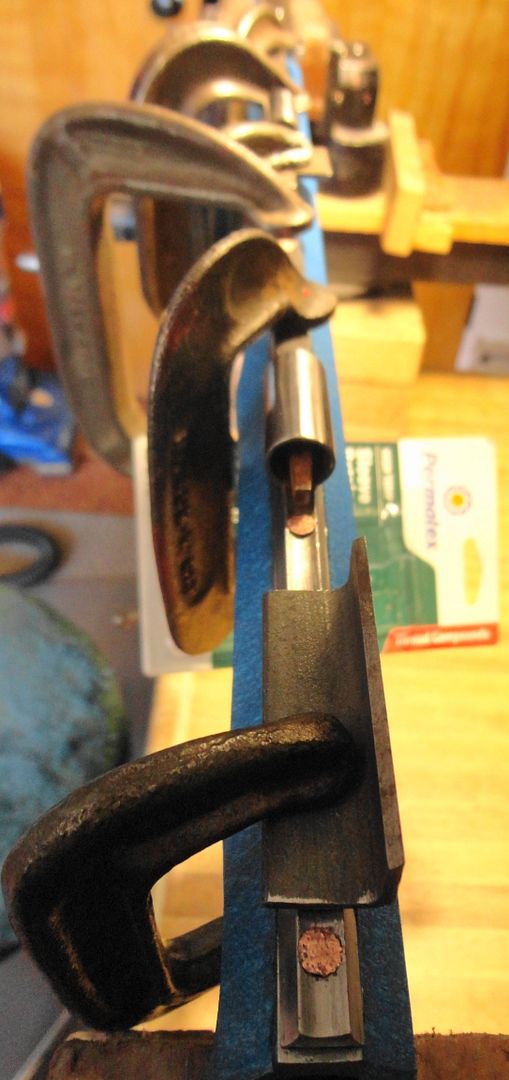