I have always done my wire inlay as Tom has described, until I had a problem with some .005" pure silver ribbon popping up after twenty years, in the cross grain of an ebony pistol grip. Going into a cut across the grain, and around a curve is the most challenging I've found thus far. I remembered an e-mail conversation I had about this topic, and I think it was from Gary Brumfield. He told be to take the ribbon and stand it on its edge on a hard surface, and tap the edge with a not too sharp knife, many times. This puts little cuts across the thin edge of the ribbon, but more importantly, creates a little burr on both sides of the ribbon. My sketch is exaggerated but shows the idea. This burred edge then goes into the cut, and when the wood is wetted, it closes on the ribbon and locks it in the slot.
So, I carefully pulled that offending "wire" out of it's place in the grip, gave it this treatment, and put it back. I had to snip off a little at the end of the inlay, as the wire had lengthened. The fix is permanent.
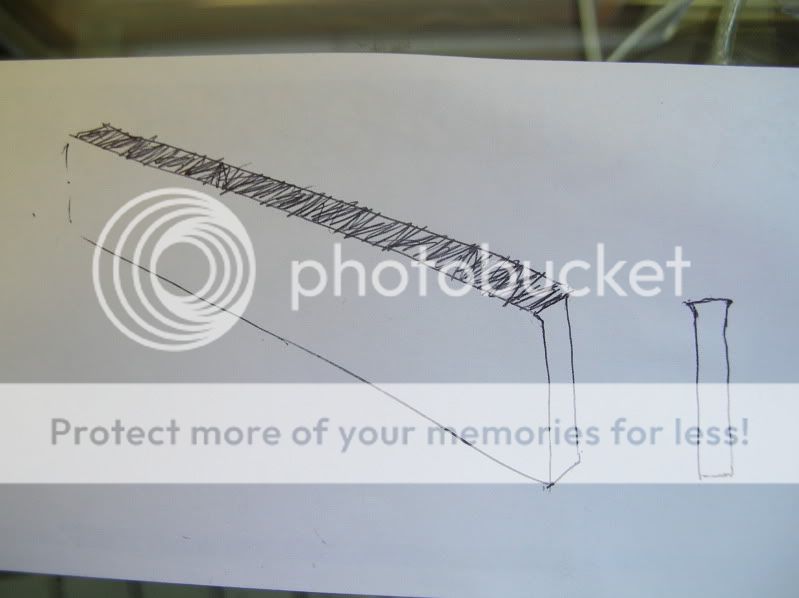