Guys,
Now to mount the newly forged cock onto the tumbler. This can be a frustrating job, but here is the way I do it. First, file a nice square onto the round tumbler shaft so that only a tiny part of the round shaft shows on the outside of the lockplate when the tumbler is assembled. This gives a tiny gap between the lockplate outside and the cock inside, so it is very close, but does not rub.
Next, how to get the hammer on in the proper orientation? The hole in the cock shows the center, but at what angle? I put a small spot of soft solder on the inside surface of the cock around the pivot hole. Next I "mount" the cock onto the assembled lockplate & tumbler. I am sure that you understand that the cock will be way far from the lockplate by about 3/16 inch or so. Now turn the cock to what will be the proper orientation. I like the cock lower jaw tip to be about 3/16 inch away from the pan fence when the tumbler is in the fully down or fired position. Reach behind the cock with a sharp pointed tool and make scratches in the soft solder all around the square of the tumbler.
Next, remove the cock and punch mark the four corners of the scratch marks. There you have the guide for the proper orientation of the square hole in the cock. Now that old familiar file-n-fit, file-n-fit, file-n-fit until the cock mates tightly with the tumbler square.
As you can see in the photo of the lock interior, I still must file back the cock inside shoulder so that the shoulder hits the lockplate top edge at the same time as the tumbler shoulder hits the bridal. Next time for that.
Jim
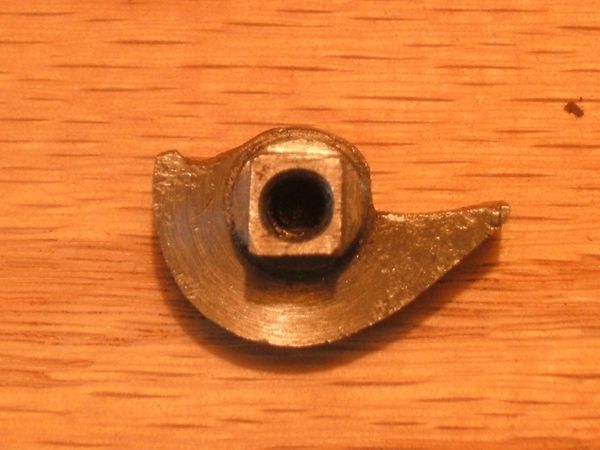
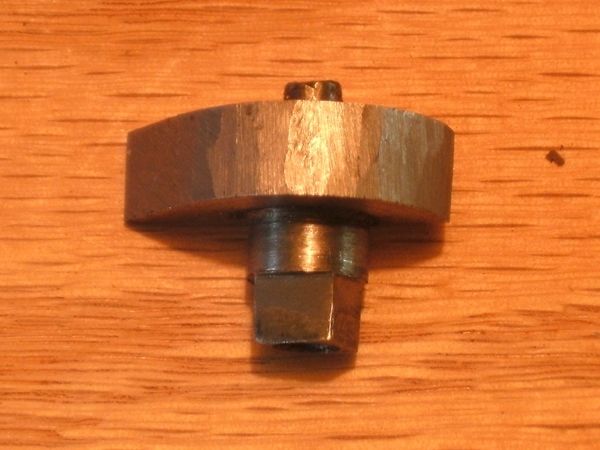
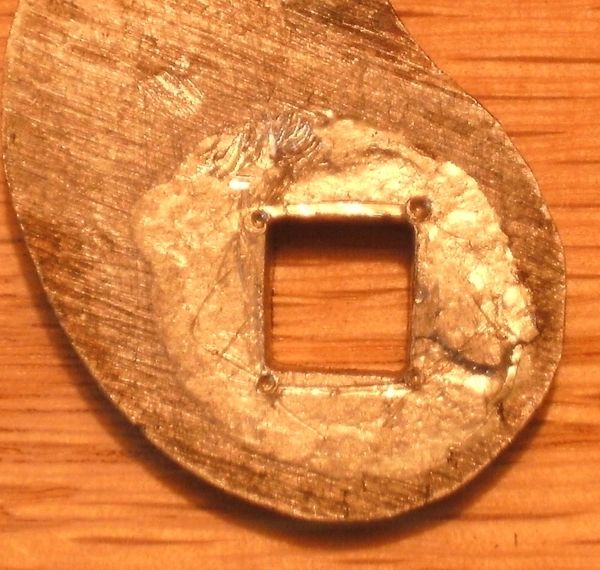
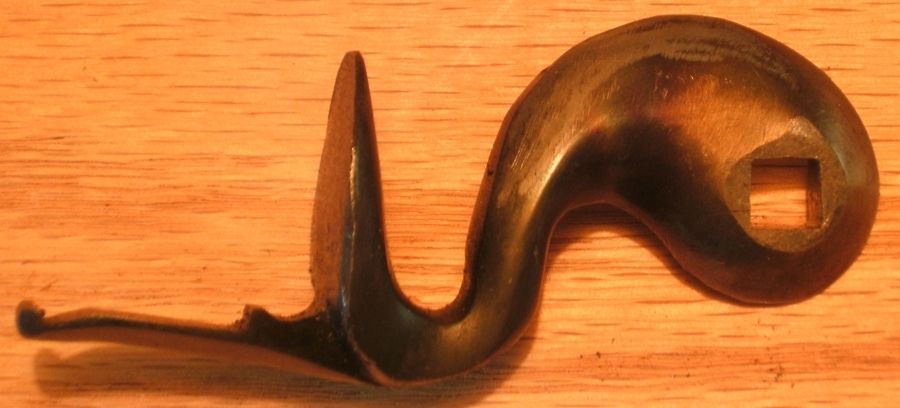
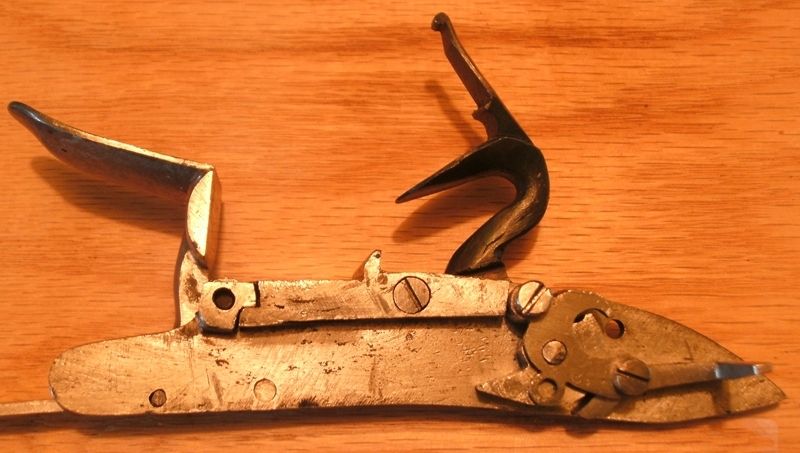
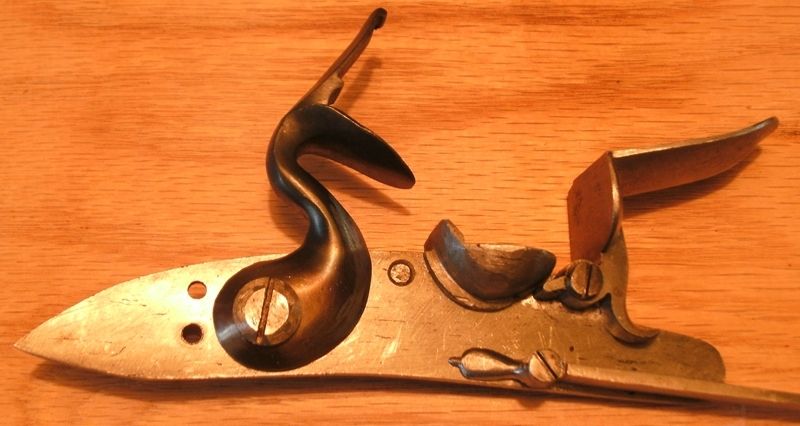